Every Good Story Starts with a Beer—and Even Better Flooring Solutions
Founded in 2014, the Detroit HopCat quickly became a landmark community watering hole. Its central location—an easy stroll to Little Caesars Arena, Comerica Park, and Ford Field—and extensive array of taps have enticed locals through the front door for nearly a decade now. But despite all this success, the iconic Detroit location was mired in an extensive remodel—one that might have forced the brewpub to temporarily shut down during construction. That’s when Kent Companies brought extensive expertise in flooring solutions to bear and kept the doors open.
The challenge for HopCat was to restore the second floor of the bar while keeping the first floor operational for the public. The Kent Companies team worked under significant constraints in terms of time, safety, and preparation; the project’s execution had to be seamless.
HopCat’s New Flooring Solutions
Kent Companies was introduced to HopCat Detroit when its previous business partner—SCI Floor Coverings—reached out regarding the project. The two struck a direct deal soon after.
It took a handful of weeks to provide an estimate, sign off on the proposal, and schedule the project. Then, Kent Companies managed to execute the job in just one day.
This timeline not only helped expedite the overall second floor renovations, but also minimized any potential disruption to the bar’s normal operations.
The overall goal for HopCat was to open the Huma Room on the second floor. The new space would feature both an outdoor patio and an iconic black 1973 Cadillac Fleetwood mounted behind the wall. To this end, Kent Companies was responsible for leveling out a 2,240 square foot area on the second floor.
Typically, the Kent Companies team would turn to gypsum-based underlayments in this scenario. However, this project occurred in July 2023, when gypsum underlayments projects were experiencing significant supply chain delays and disruption. At the same time, the fact that customers and staff would be on the first floor the day of the project made leak prevention essential.
Kent Companies recommended an ideal solution for this scenario. Schonox APF 4,000 PSI synthetic-reinforced underlayment can pour over wood at 3/8 inch and hardens quickly—making it a more than suitable alternative. On the day of the project, Kent Companies first prepared the floor with Schonox prime and fill; after this set, they quickly applied the self-leveling compound.
This strategic approach to finding the right materials at the right time allowed the Kent Companies team to pull off the day’s work without disrupting the customers below.
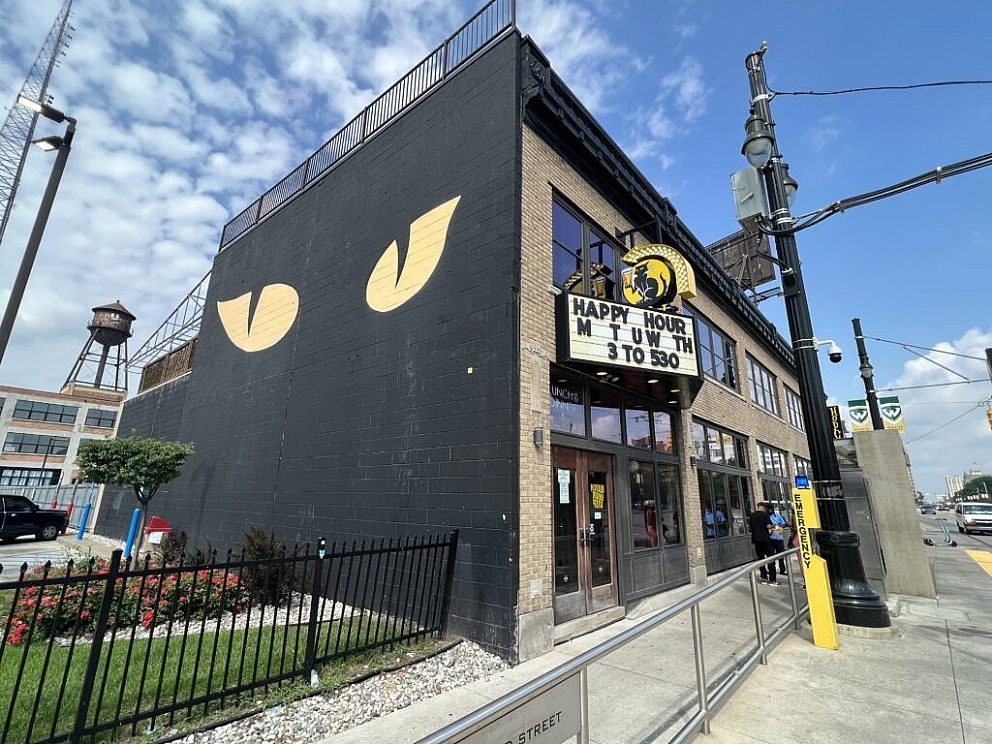
Project Challenges
HopCat’s project required the Kent Companies team to pour the underlayment on the second floor above the bustling bar. This challenge added an inherent degree of complexity to the entire process.
The fact that the bar would be open meant the on-site team needed to use precision with every step of the process. They needed to ensure all occupants of the building were safe and comfortable, so as not to disrupt the day’s business.
Kent Companies knew that extensive preparation before arriving at the worksite was critical in this scenario. Our approach extended beyond typical safety protocol on a construction site. The team needed to thoroughly separate the public from the construction zone.
Knowing that time was of the essence, Kent Companies handled the challenge by selecting products that were not just fast-drying, but also applied rapidly—thus the pivot to Schonox APF 4,000 PSI synthetic reinforced underlayment.
Establishing a detailed blueprint for the day’s operations ahead of time also prepared the team for success. From setting up equipment on a closed side street to carefully maneuvering around HopCat’s space to stay out of patrons’ way, Kent Companies ensured that the bar could operate as normal on the day of the project.
Transitions and Elevation Matching
Proper elevation matching and comprehensive transition filling is a critical component of flooring solutions. This not only aesthetically rounds out the space to provide a cohesive look, but also ensures that the room is functionally seamless—and thus safe—for future occupants.
In addition, the focal point of HopCat’s second floor is the bar. Given its prominence, achieving a flawless transition here was of the utmost importance. The challenge was twofold. First, the team had to ensure that the bar area seamlessly merged with its surroundings. Second, they needed to confirm that any elevation differences were imperceptible to the eye and foot.
HopCat is located in a historical building, which further adds to the skill and craftsmanship required to create matching transitions. Any variation in riser heights or tread depths in a stairwell must be accounted for; therefore, the team paid exacting attention to providing flooring solutions that elevate the history of the building, while providing transitions that meet and exceed modern standards. Critically, this is why Kent Companies specifically chose Schonox APF—for its thin, even spread.
Using strategic zones like stairwells, door landings, and the bar area as target points, Kent Companies effectively navigated the challenges presented by the property, underscoring proficiency in handling complex renovations.
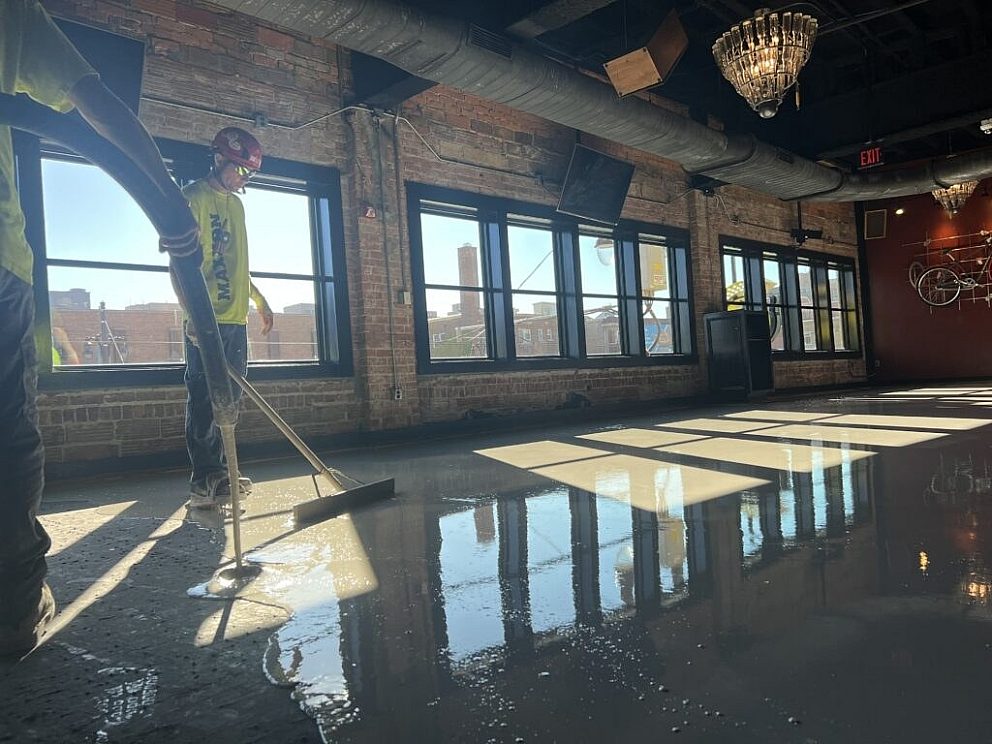
Learning and Results
The HopCat project exemplifies Kent Companies’ adaptability in the face of unique circumstances. The choice to pivot from typical gypsum-based underlayment to Schonox APF proved key in operational planning, allowing for smooth execution despite the project’s constraints.
Execution of the project in just one day further highlights the team’s efficiency. Thanks to a careful planning process that incorporated a strategic material selection, Kent Companies conducted the on-site work went off without a hitch.
The HopCat project also underscores the significance of combining correct product specifications and strategic operational planning. This project serves as proof that renovations can be strategically implemented while maintaining business continuity. It takes a partner like Kent Companies to make it happen.